Digitale Ordnung statt Kabelgewirr
Erlanger Uni-Lehrstuhl holt Fertigung von Pkw-Bordnetzen zurück nach Deutschland
23.8.2023, 10:49 Uhr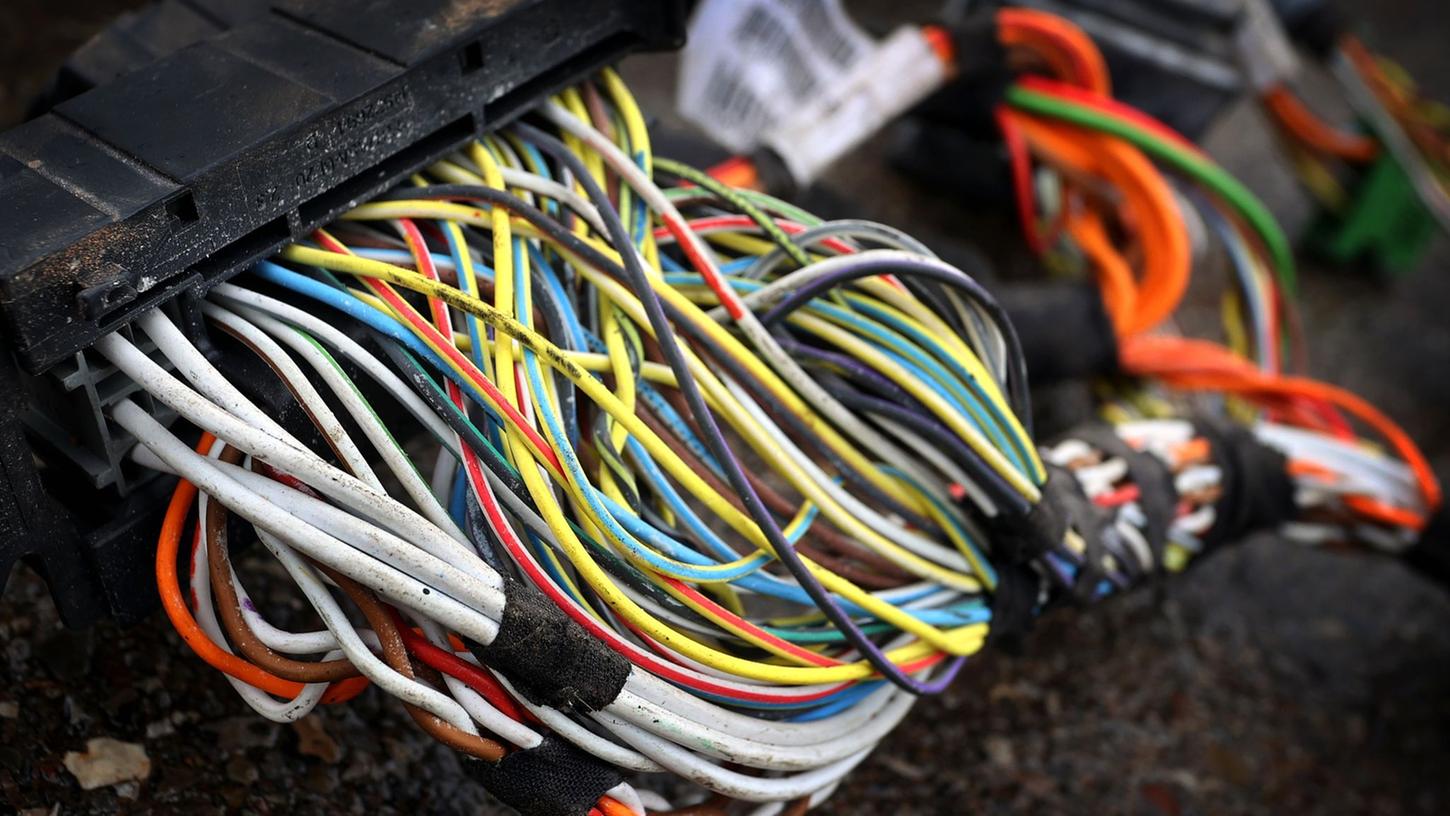
Spätestens mit der Vorfahrt für E-Autos erhalten die Pkw-Bordnetze eine zentrale Rolle. Das Kabelgewirr in jedem Auto steht für die steigende Elektrifizierung der Autos und wird einmal mit sicherheitskritischen Funktionen das autonome Fahren ermöglichen. Damit wird das Bordnetz endgültig zum Nervensystem der Mobilität.
Bislang ist die Produktion von diesen Leitungssatzsystemen ein personalintensiver Prozess mit geringer Automatisierung. Forschende der Friedrich-Alexander-Universität Erlangen-Nürnberg (FAU) wollen nun im Rahmen des Forschungsprojekts „Next2OEM“, gefördert vom Bundesministeriums für Wirtschaft und Klimaschutz, die gesamte Wertschöpfungskette durchleuchten, digitalisieren und automatisieren. Damit lässt sich zugleich das Gewirr aus Prozessschritten und Zuständigkeiten auflösen.
Komplexe Nervenbahnen im Bordnetz
Am Ende des Projekts des Lehrstuhls Fertigungsautomatisierung und Produktionssystematik (FAPS) steht eine prototypische Umsetzung, die die Fertigung der Bordnetze als „Made in Germany“ zurück nach Deutschland holt. Das Projekt Next2OEM und hat ein Gesamtvolumen von über 24 Millionen Euro und wird im Januar 2026 abgeschlossen.
Bordnetze sind für Autofahrerinnen und -fahrer eine Art Black Box, denn die innen verbauten Bordnetze sind für sie praktisch unsichtbar. Dabei bilden die kundenspezifischen Leitungssätze ein komplexes Nervensystem für ein Fahrzeug. Bereits in einem mittelgroßen Pkw finden sich durchschnittlich rund 3000 Einzelleitungen, die mit weiteren Bordnetzkomponenten auf ein Gesamtgewicht von 55 Kilo kommen.
Kabel werden quer durch die ganze Welt transportiert
Die Wertschöpfungskette ist in der Vergangenheit bei den Produkt- und Prozessstrukturen einfach mitgewachsen, ohne es von Grund auf neu zu denken. So sorgte etwa das Primat der Kosteneffizienz zu einer überbordenden Logistik. Angesichts günstiger Kostenstrukturen haben sich etwa Nordafrika und die Ukraine als Fertigungsstandorte etabliert. Das kann in einzelnen Fällen dazu führen, dass Kabel und kleinere Bauteile mehrfach quer durch die ganze Welt transportiert werden, bevor es hierzulande zur Endmontage bei einem Hersteller (OEM) ankommt. Mit der russischen Invasion in der Ukraine wurde die fehlende Resilienz dieser Lieferketten sichtbar. Insbesondere während der Corona-Pandemie zeigte sich die Fragilität der Beschaffungsprozesse.